AI inference for Smart Manufacturing
Creating breakthroughs in efficiency, accuracy, and quality
Sensing and AI inference replacing tedious programming
AI has many applications in sorting through volumes of big data coming from manufacturing floors today. At the edge, higher speed, higher resolution sensors including video reveal more about processes and product quality than ever. Instead of creating and programming complex models, manufacturers are turning to edge AI inference to quickly judge outcomes, predict movements, and meet goals.
Smart Manufacturing Use Cases
Historically, human inspectors did meticulous, hands-on inspection of finished goods, gauging conformance to desired quality. Not only are these techniques time-intensive, they can be mind numbing with hour-after-hour, day-after-day repetition.
Increasing throughput requires automation of visual inspection techniques. Ideally, goods can be inspected as they flow through the production line, even at each step. Rejecting flawed goods sooner in the process reduces costs, simplifying rework and preventing accumulation of errors. High-resolution video can spot minute anomalies or flaws.
Maximizing productivity means running AI-based visual inspection at the pace of production, making decisions within a short period of time as goods appear. Automation never tires, and makes equally good decisions at the beginning and end of a shift.
Robotics programming is an artform. Conventional industrial automation robots with six degrees of freedom have their own programming languages and syntax. There are also many rules, particularly around safety of movements preventing damage or harm.
Programming involves a lot of trial and error. Understanding both the process steps and the manipulation capability of the robot is required for successful configuration. Robotic programming is only as good as the programmer’s ability to foresee and code for any unexpected situations.
One technique gaining momentum is human-guided learning, where a human demonstrates the motions for the robot. Also in play are unsupervised learning techniques such as generative adversarial networks (GANs), These techniques focus on reducing the time and effort needed to bring a robot up to speed.
In a modern manufacturing environment, robots generally do not work alone. Multiple robots engage in a sequence of activities, and sometimes several robots work in coordination on a single step of the process. Robots may also be involved in fetching raw materials and shuttling them to the production line, like in an automated warehouse.
How robots choose their path of motion can make a huge difference in throughput and efficiency. It’s not unlike the requirements for self-driving cars, albeit on a closed circuit under much more controlled conditions. Robots must understand a map from start to destination, and navigate successfully while avoiding collisions.
AI inference enables perception, prediction, and planning phases needed to sense objects and make motion decisions, and can help learn the most efficient paths.
SAKURA-II M.2 Modules and PCIe Cards
EdgeCortix SAKURA-II can be easily integrated into a host system for software development and AI model inference tasks.
Order an M.2 Module or a PCIe Card and get started today!
EdgeCortix Edge AI Platform
Full-Stack Solution: Integrated Platform Increases Ecosystem Value Over Time
Unique Software
Proprietary Architecture
AI Accelerator
Efficient Hardware
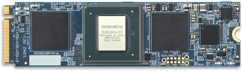
Modules and Cards
powered by the latest SAKURA-II
AI Accelerators
Deployable Systems
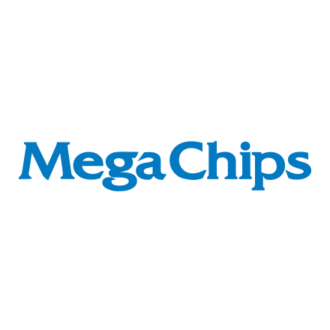
Given the tectonic shift in information processing at the edge, companies are now seeking near cloud level performance where data curation and AI driven decision making can happen together. Due to this shift, the market opportunity for the EdgeCortix solutions set is massive, driven by the practical business need across multiple sectors which require both low power and cost-efficient intelligent solutions. Given the exponential global growth in both data and devices, I am eager to support EdgeCortix in their endeavor to transform the edge AI market with an industry-leading IP portfolio that can deliver performance with orders of magnitude better energy efficiency and a lower total cost of ownership than existing solutions."
Improving the performance and the energy efficiency of our network infrastructure is a major challenge for the future. Our expectation of EdgeCortix is to be a partner who can provide both the IP and expertise that is needed to tackle these challenges simultaneously."
With the unprecedented growth of AI/Machine learning workloads across industries, the solution we're delivering with leading IP provider EdgeCortix complements BittWare's Intel Agilex FPGA-based product portfolio. Our customers have been searching for this level of AI inferencing solution to increase performance while lowering risk and cost across a multitude of business needs both today and in the future."
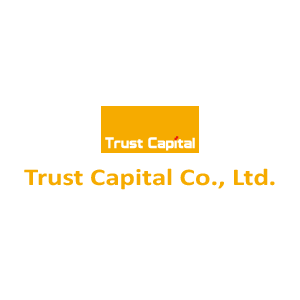
EdgeCortix is in a truly unique market position. Beyond simply taking advantage of the massive need and growth opportunity in leveraging AI across many business key sectors, it’s the business strategy with respect to how they develop their solutions for their go-to-market that will be the great differentiator. In my experience, most technology companies focus very myopically, on delivering great code or perhaps semiconductor design. EdgeCortix’s secret sauce is in how they’ve co-developed their IP, applying equal importance to both the software IP and the chip design, creating a symbiotic software-centric hardware ecosystem, this sets EdgeCortix apart in the marketplace.”